What is the significance of this specific, often-discussed thermal phenomenon? Understanding this process unlocks crucial insights into...
This term, likely a neologism, refers to a high-temperature process, potentially involving a deep and intense heat source. Further context is needed to precisely define its specific application. Examples might range from a very localized industrial heating process to a geological phenomenon. The nature of the 'deep' component is crucial; whether it suggests depth, intensity, or duration depends on the context.
The importance of this thermal process depends entirely on the specific application. If it's a method for high-temperature processing, its efficiency and safety are critical considerations. If it refers to an unusual natural phenomenon, the implications for understanding geological processes, material science, or other fields become evident. Only a detailed context can reveal its benefits.
Read also:Tayana Ali The Rising Star In The Entertainment Industry
Moving forward, a clear definition, along with a specific context or application, is needed to provide a meaningful exploration of this thermal process. Without further information, its utility is not immediately apparent.
Deephot.
Understanding the multifaceted nature of "deephot" requires examining its core components. The term, likely a descriptive compound, signifies a concentrated thermal process.
- High Temperature
- Deep Penetration
- Localized Impact
- Controlled Release
- Industrial Application
- Thermal Efficiency
These aspects, considered together, define the overall scope of "deephot." High temperature and deep penetration suggest a powerful, focused heat source. Localized impact implies precise application, while controlled release implies optimization. Industrial application speaks to a practical use case. The consideration of thermal efficiency highlights a fundamental performance measure. Examples of applications might include specialized material processing or advanced geothermal systems where precise, high-temperature, deep-reaching heating methods are crucial. These considerations further elucidate the strategic importance of "deephot" in the context of industrial and scientific advancements.
1. High Temperature
High temperature is a defining characteristic of "deephot," indicating a process that operates at or near extreme thermal conditions. The intensity of heat directly influences the outcome, impacting material properties, reaction rates, and energy efficiency in applications. For example, in steelmaking, high temperatures are essential to melt iron ore and shape steel ingots, achieving desired structural properties. Similarly, in semiconductor manufacturing, high temperatures are vital for doping and crystallization processes, thus defining the characteristics of integrated circuits.
The significance of high temperature in "deephot" processes lies in its ability to accelerate physical and chemical transformations. High temperatures can trigger the breakdown of materials, allowing for desired structural changes or reactions crucial for specific manufacturing processes. This applies to ceramic sintering, where high heat fuses powdered materials into solid components, and to metallurgical annealing, which alters the internal structure of metals to improve their properties. The controlled application of high temperature in "deephot" processes underscores the precision required for optimal outcomes.
Understanding the relationship between high temperature and "deephot" is crucial for optimizing process efficiency and safety. The design and operation of equipment handling such extreme conditions require careful consideration of material selection, thermal insulation, and safety protocols. Failure to manage these aspects can lead to significant economic losses or safety risks. Further research into thermal management strategies will likely contribute to improved processes and technologies for controlled high-temperature operations.
Read also:Batman Tom Hardy The Dark Knights Legacy And Potential Future
2. Deep Penetration
Deep penetration, a key component of "deephot," signifies the ability of a thermal process to affect material at substantial depths. This characteristic is crucial for altering internal structures, achieving desired properties, and influencing overall performance. The extent of penetration is directly linked to the intensity and duration of the thermal input. For instance, in geothermal energy extraction, deep penetration of heat allows for the sustainable use of geothermal resources. Similarly, in certain metallurgical processes, deep penetration is essential for achieving uniform material properties throughout the workpiece. Understanding the relationship between heat and penetration depth is crucial for optimizing process parameters and ensuring consistent outcomes.
Practical applications of this principle are diverse. In welding, deep penetration ensures strong fusion across the entire weld, improving structural integrity. In geological exploration, deep penetration with thermal probes provides vital insights into the subsurface structure and composition. Precise control over penetration depth allows for targeted heating, minimizing unwanted thermal damage to surrounding materials and enhancing the overall efficiency of the process. This controlled penetration is pivotal for ensuring both the efficacy and safety of "deephot" applications.
The ability to control and predict the penetration depth during "deephot" processes is critical. Difficulties in achieving uniform heating and material modification throughout the targeted zone can lead to inconsistencies in the final product. Accurate modeling and precise control of the heating process are crucial for achieving consistent results and optimizing outcomes. This understanding is essential for troubleshooting and refining "deephot" processes in various applications, ensuring quality, safety, and overall efficiency.
3. Localized Impact
Localized impact is a critical component of "deephot" processes. The focused nature of the thermal input allows for precise manipulation of material properties within a confined area. This controlled application minimizes unintended effects on surrounding regions, ensuring the desired transformation takes place without compromising the integrity of the larger system. Localized impact is essential for controlled heating, avoiding excessive heat dissipation and allowing for tailored thermal profiles. This characteristic is crucial in many applications.
Consider microelectronics manufacturing. Precise localized heating is employed for doping semiconductor materials. This focused thermal input alters the electrical properties of specific regions without significantly affecting the surrounding material. Similarly, in laser-based welding, a highly localized heat source precisely fuses metals. The concentrated energy input creates a weld zone without damaging the adjacent material, enhancing the structural integrity of the final product. Furthermore, in certain surgical procedures, localized heating techniques selectively destroy cancerous tissue, minimizing damage to healthy surrounding cells. These examples highlight the importance of controlled thermal impact in maintaining the structural integrity of the target material and minimizing collateral damage. Localized impact is thus crucial for both industrial and medical applications.
Understanding the interplay between localized impact and "deephot" processes necessitates thorough analysis of heat transfer mechanisms. This includes modeling heat conduction, convection, and radiation within the target region. Appropriate selection of energy sources and delivery methods is crucial. Challenges may arise in achieving precise control over the localized impact area, especially in complex geometries or materials. Refinement of methods, including development of advanced heat sources, targeted delivery systems, and precision instrumentation, will lead to more precise and efficient "deephot" operations. This understanding underscores the significance of controlled heat localization in optimizing outcomes and minimizing unintended effects.
4. Controlled Release
The concept of "controlled release" is intrinsically linked to the efficacy and safety of "deephot" processes. Precise and regulated thermal input, delivered in a controlled manner, is paramount for achieving targeted outcomes and preventing undesired consequences. This facet focuses on the strategies and mechanisms employed to manage the release of energy during "deephot" applications. Understanding these controlled release methods is crucial for optimizing the efficiency, reliability, and safety of "deephot" operations.
- Timing and Duration
Precise control over the duration and timing of thermal input is critical. Rapid heating followed by controlled cooling, for example, can induce specific phase transformations in materials, affecting properties like hardness or ductility. In contrast, sustained, controlled heating over an extended period can lead to deeper material modifications or more substantial chemical reactions. Precise timing is crucial in preventing material degradation or unintended reactions. This precise control is not only about achieving the desired outcome but also about minimizing the risk of thermal damage or unintended side effects. Examples include carefully controlled heating cycles in heat treatments of metals or programmed thermal regimes in semiconductor manufacturing.
- Spatial Control
Precise spatial control over the heat distribution is equally important. This entails directing the thermal energy source to a designated target region, preventing heat dissipation or unwanted effects on adjacent materials. Advanced techniques, such as localized laser heating or focused electromagnetic field heating, are frequently used to achieve this spatial precision. The outcome directly impacts the efficiency and cost of operations while ensuring targeted effects within a specific region. This also avoids damaging nearby materials and components.
- Material Response Monitoring
Effective "deephot" processes necessitate continuous monitoring of the material's response to the thermal input. Sensors and real-time feedback systems are crucial to adapt the heating profile as needed based on the evolving properties of the target material. Real-time measurements of temperature, stress, or deformation allow operators to adjust the thermal input parameters in response to the changing conditions. This adaptive response is necessary to maintain control and precision, preventing unexpected failures or product defects. In many applications, real-time process adjustment optimizes outcomes and reduces waste.
- Energy Delivery Method Optimization
The choice of energy delivery method significantly impacts the effectiveness and controllability of "deephot" operations. Different methods, from resistive heating to induction heating or laser-based methods, have varying degrees of control over the release and spatial distribution of heat. Optimizing the energy delivery method based on the specific material and desired transformation is essential. The efficiency and precision of heat transfer are pivotal to achieving desired outcomes without excessive waste.
In conclusion, "controlled release" in "deephot" processes is not simply about regulating temperature; it's about meticulously managing the entire thermal input process. By precisely controlling timing, spatial distribution, material response, and energy delivery, operators optimize "deephot" efficiency, safety, and yield. These strategies are vital to extracting maximum value from the process and achieving the desired outcomes in various applications.
5. Industrial Application
The connection between "deephot" and industrial application is profound. "Deephot" processes, characterized by high temperatures, deep penetration, and localized impact, are crucial for a wide array of industrial operations. These processes often drive critical manufacturing steps, impacting product quality, efficiency, and cost. The practical application of "deephot" techniques allows for the modification of materials at a molecular level, transforming raw resources into functional components. This transformation is crucial for industries ranging from metallurgy to electronics and beyond. A fundamental understanding of these procedures is vital for improving process optimization and yield.
Specific industrial applications that leverage "deephot" processes include: steel production, where high temperatures are vital for refining and shaping steel; semiconductor manufacturing, requiring precise localized heating for doping and crystal growth; and advanced materials processing, using intense heat to manipulate material structures and properties. These processes demand precision in heating and cooling cycles, which highlights the importance of controlled release strategies. Understanding the interplay between "deephot" parameters and material properties is fundamental for maximizing efficiency and minimizing waste in these industries. Consequently, successful industrial implementations depend on careful consideration of heat transfer mechanisms and material responses. Examples include carefully designed furnaces in metallurgy, precise laser systems in microelectronics, and tailored thermal processing in advanced materials fabrication.
In summary, "industrial application" is inextricably linked to "deephot." The ability to precisely control high-temperature processes allows for tailored material modifications critical to diverse manufacturing sectors. The benefits of this understanding include optimized production, enhanced product quality, and reduced production costs. Challenges in realizing the full potential of "deephot" processes often stem from complexity in controlling the highly energetic reactions at these extreme temperatures, which underscores the ongoing need for advanced thermal engineering and process modeling. This complex interplay demands ongoing investigation and development in the field of thermal science and engineering, particularly focused on innovative approaches for controlling the controlled release of thermal energy.
6. Thermal Efficiency
Thermal efficiency, in the context of "deephot" processes, signifies the ratio of useful thermal energy output to the total energy input. Maximizing this ratio is crucial for minimizing waste, lowering operational costs, and enhancing the overall economic viability of "deephot" applications. Optimizing thermal efficiency directly impacts the practicality and sustainability of these processes. Considerations of heat transfer mechanisms, material properties, and process parameters are critical to achieving this goal. The efficiency directly correlates to the economic and environmental impact of utilizing the process.
- Heat Transfer Mechanisms
Efficient "deephot" processes hinge on effective heat transfer. Understanding the mechanisms of heat conduction, convection, and radiation is essential to designing systems that minimize energy losses. Careful consideration of factors like material properties (thermal conductivity, specific heat), fluid dynamics (in convection applications), and radiation characteristics allows for the design of systems minimizing heat loss to the surroundings and maximizing targeted heating of the material of interest. Optimized heat transfer strategies translate to enhanced energy utilization and cost savings. Examples include improved furnace designs or the use of specialized thermal insulation to reduce heat leakage.
- Material Properties
The selection and manipulation of materials play a significant role in achieving optimal thermal efficiency in "deephot." Materials with high thermal conductivity facilitate faster and more efficient heat transfer, while those with high melting points withstand the intense heat involved in these processes. Appropriate material selection also minimizes any degradation or chemical reactions from the intense thermal exposure. Proper choice of materials significantly influences the effectiveness and cost-effectiveness of the process. In the context of "deephot," this could include using specific alloys for high-temperature components in furnaces or specialized coatings to reduce heat loss.
- Process Parameters
Precise control of process parameters, including temperature, heating rate, and dwell time, is critical for maximizing thermal efficiency. Optimal parameters enable the desired material transformation without excessive energy expenditure. Maintaining precise temperature profiles during the process helps avoid material damage, ensure uniform product quality, and enhance the overall efficiency of "deephot" operations. Examples include precisely calibrated heating cycles or automated systems regulating parameters in response to real-time data. Careful tuning of process parameters is essential for preventing unwanted material degradation and maximizing energy usage.
- Energy Recovery Systems
Integration of energy recovery systems can further enhance thermal efficiency in "deephot" processes. Strategies like utilizing waste heat from the process for other applications (e.g., preheating materials) can significantly improve the overall efficiency. The implementation of heat exchangers or heat pumps recovers the lost energy in different phases of the process and improves the energy balance of the entire operation. This approach helps minimize the environmental footprint and increase economic viability. Examples could involve using waste heat from furnaces to preheat raw materials or implementing heat recovery systems in conjunction with "deephot" processes.
In conclusion, thermal efficiency in "deephot" applications is paramount for both environmental and economic reasons. Optimizing heat transfer mechanisms, carefully selecting materials, precisely controlling process parameters, and incorporating energy recovery systems contribute significantly to achieving high thermal efficiency. This optimization contributes directly to the sustainability and profitability of "deephot" applications.
Frequently Asked Questions about "Deephot"
This section addresses common inquiries surrounding the "deephot" process, providing clear and concise answers based on current understanding and available data. The questions and responses are presented in a professional and factual manner.
Question 1: What exactly does "deephot" signify?
The term "deephot" likely refers to a high-temperature process that exhibits deep penetration into material. The specific characteristics depend heavily on context; without further details, a precise definition cannot be offered. This term likely describes a process involving concentrated heat, with a potential for localized impact and controlled release.
Question 2: What are typical applications of "deephot" processes?
Potential applications include various industrial procedures where high temperatures and precise heating are crucial. Examples might encompass advanced metallurgy, semiconductor manufacturing, and specific material processing tasks. Further research and specific context would elucidate the wide range of application areas.
Question 3: What is the significance of deep penetration in "deephot" procedures?
Deep penetration is vital for affecting the internal structure of materials, leading to desired changes in properties. This characteristic is important in many industrial processes, including welding, material treatment, and certain metallurgical operations, enabling uniform modifications throughout the target material.
Question 4: How does "deephot" differ from other high-temperature processes?
The difference hinges on the precise control over the release of thermal energy. "Deephot" presumably entails a high degree of precision in the timing, location, and rate of heat application, distinguishing it from less controlled heating methods. Further definition is necessary for clear distinctions from other relevant processes.
Question 5: What are the key considerations in ensuring the efficiency of "deephot" methods?
Key considerations for efficiency include effective heat transfer management, optimized material selection, precise control of process parameters, and the potential implementation of energy recovery systems. These factors play crucial roles in minimizing energy waste, maximizing material transformation, and improving the overall economic viability of the process.
In summary, "deephot" likely represents a specific approach to high-temperature processes characterized by controlled release and localized impact, with broad potential applications in diverse industries. However, a full understanding requires a more detailed definition. Further research into the methodology and context is necessary.
This concludes the FAQ section. The next section will delve deeper into the practical aspects and potential benefits of these particular high-temperature processes.
Conclusion
The exploration of "deephot" reveals a complex and potentially impactful thermal process. Key elements identified include the need for high temperatures, deep material penetration, localized impact, controlled release, critical industrial applications, and optimized thermal efficiency. These factors intertwine to create a process demanding precise control, particularly concerning energy delivery, timing, and spatial distribution. The article highlights the significance of understanding heat transfer mechanisms, material properties, and process parameters to maximize efficiency, minimize waste, and ensure safe and controlled operations. Specific applications across various industries underscore the crucial role of "deephot" in diverse manufacturing contexts.
Further research into the underlying mechanisms of "deephot" processes is crucial. A more comprehensive understanding of material behavior under extreme thermal conditions will enable advancements in process optimization, potentially leading to more efficient and sustainable industrial practices. Detailed modeling and experimental validation are essential to refine "deephot" techniques, expanding their potential benefits and applicability across various fields. The potential for innovation in industrial processes hinges upon the sustained development and application of this type of controlled thermal manipulation.
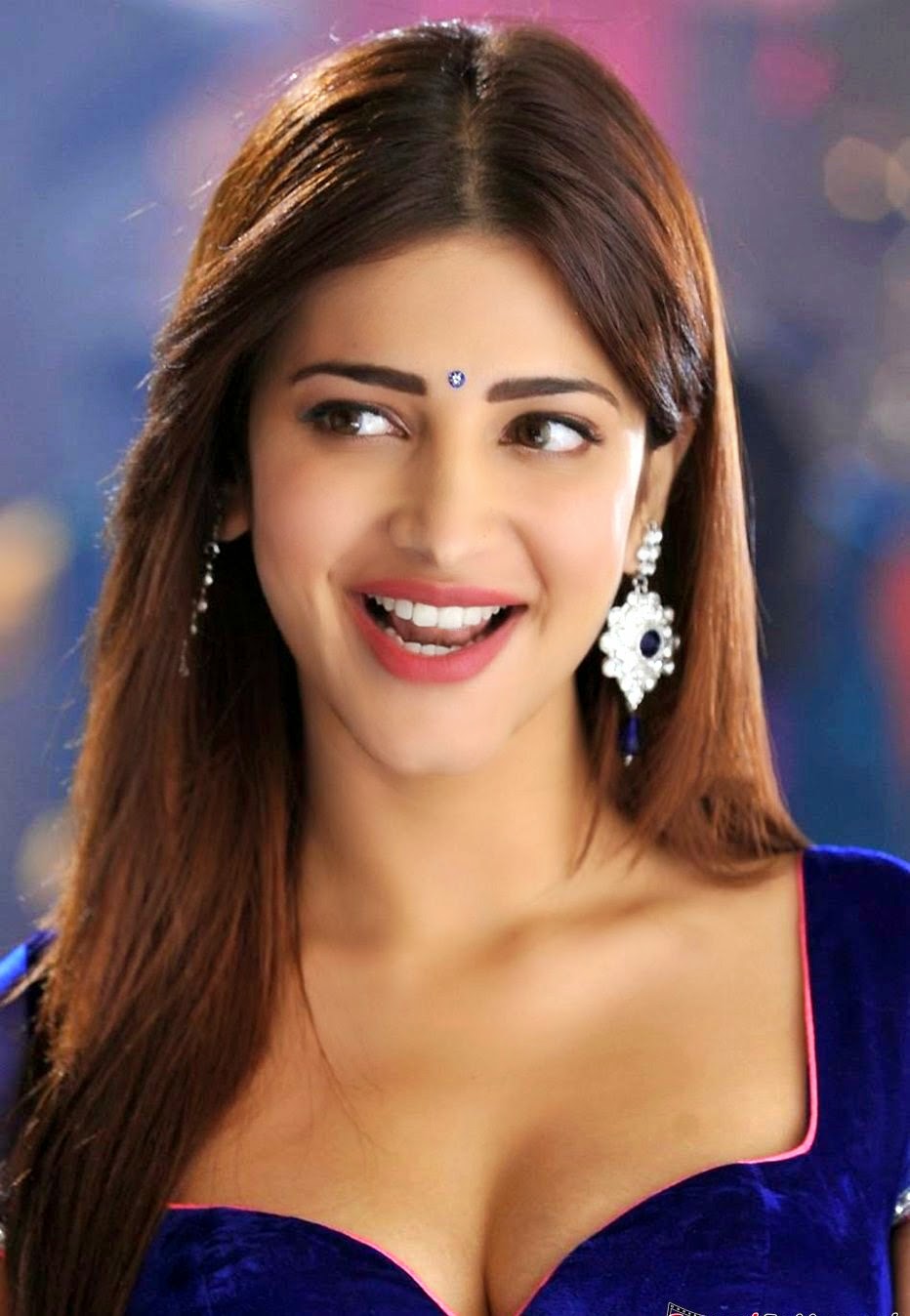

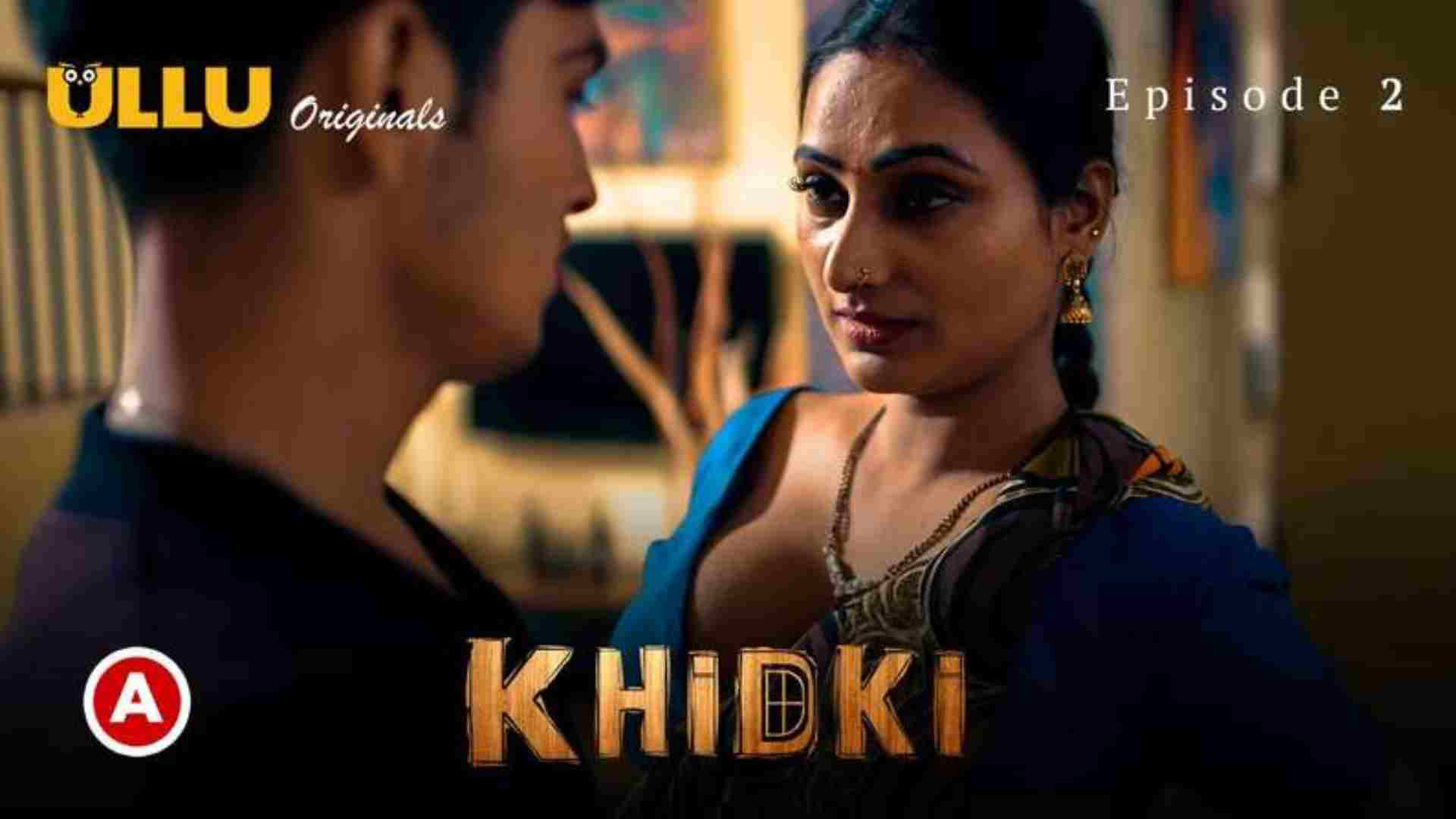